What is Industrial Refrigeration?
This comprehensive guide explores what industrial refrigeration is, its applications, and importance for Ontario businesses. It covers key components, system types, benefits, challenges, and emerging trends in the industry. The article emphasizes the crucial role of experienced contractors like GA Enns.
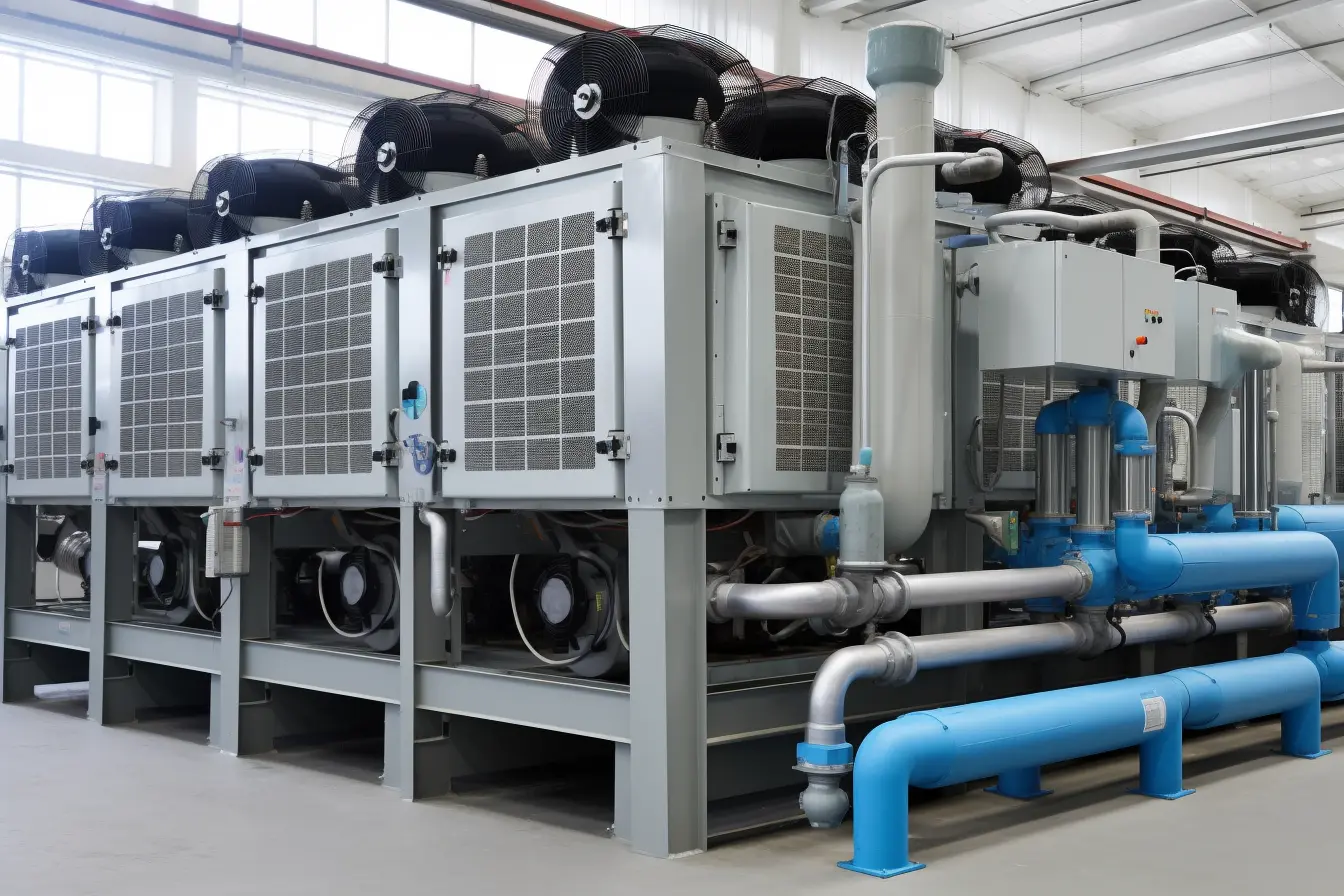
Industrial refrigeration forms the backbone of numerous commercial and industrial operations worldwide. Unlike residential cooling systems, these large-scale solutions are designed to handle massive capacities and operate in demanding environments, playing a crucial role in various sectors from food processing to pharmaceutical manufacturing.
At its core, industrial refrigeration encompasses the design, installation, and maintenance of complex cooling systems that ensure consistent temperatures for critical processes and storage. These systems not only drive productivity and product quality but also contribute significantly to regulatory compliance and energy efficiency in industrial settings.
In this article, we'll cover the key components of industrial refrigeration systems, explore their diverse applications across different industries, and discuss the benefits of implementing efficient cooling solutions. We'll also examine emerging trends in the field and provide insights on choosing the right industrial refrigeration contractor for your specific needs.
What Exactly is Industrial Refrigeration?
Industrial refrigeration refers to large-scale cooling systems designed for commercial and industrial applications. Unlike your home refrigerator, these systems are built to handle massive capacities and operate in demanding environments.
Key Components of Industrial Refrigeration Systems
- Compressors: The heart of the system, compressing refrigerant gas.
- Condensers: Where the compressed gas releases heat and condenses into a liquid.
- Evaporators: Where the liquid refrigerant absorbs heat and evaporates.
- Expansion valves: Control the flow of refrigerant into the evaporator.
- Refrigerants: The working fluid that circulates through the system.
At GA Enns, we specialize in designing and maintaining systems with these components to ensure optimal performance for our clients.
Here's a more detailed breakdown of each the main components of industrial refrigeration systems:
Compressor
The compressor is the powerhouse of any industrial refrigeration system, tasked with compressing the refrigerant and propelling it through the entire system. In the industrial refrigeration cycle, the compressor is pivotal in maintaining the necessary pressure and temperature of the refrigerant, ensuring the system operates efficiently and effectively.
There are several types of compressors used in industrial refrigeration systems, each with its own set of advantages. Reciprocating compressors are known for their reliability and are often used in smaller systems. Screw compressors, on the other hand, are favored for their efficiency and are commonly found in larger systems, including ammonia refrigeration systems. Centrifugal compressors are ideal for very large-scale cooling systems due to their ability to handle high volumes of refrigerant.
Choosing the right compressor is crucial for the specific requirements of your industrial refrigeration application. For instance, in ammonia refrigeration systems, screw or reciprocating compressors are typically used to handle the high pressure and temperature demands. These compressors are usually driven by electric motors or diesel engines and are equipped with cooling systems to prevent overheating, ensuring the longevity and efficiency of the refrigeration system.
Condenser
The condenser is another vital component of an industrial refrigeration system, responsible for cooling the hot refrigerant gas and condensing it into a liquid. In the industrial refrigeration cycle, the condenser plays a critical role in removing unwanted heat from the system, thereby maintaining the temperature and pressure of the refrigerant.
There are several types of condensers used in industrial refrigeration systems, each suited to different environmental conditions and applications. Air-cooled condensers are the most common and are typically used in environments where the ambient temperature is relatively low. These condensers rely on air to dissipate heat and are often found in smaller industrial refrigeration systems.
Water-cooled condensers, on the other hand, are used in applications where the ambient temperature is higher. These condensers use water to absorb and remove heat, making them ideal for large-scale cooling systems. Evaporative-cooled condensers are designed for environments with very high ambient temperatures. They combine air and water cooling methods to maximize efficiency and are commonly used in industrial refrigeration plants.
Metering Device
The metering device is a critical component of an industrial refrigeration system, responsible for regulating the flow of refrigerant into the evaporator. In the industrial refrigeration cycle, the metering device ensures that the refrigerant is delivered at the correct rate, maintaining the pressure and temperature needed for efficient operation.
There are several types of metering devices used in industrial refrigeration systems. Expansion valves are the most common, used in applications where the refrigerant flow rate is relatively low. These valves precisely control the amount of refrigerant entering the evaporator, optimizing the refrigeration cycle.
Capillary tubes are another type of metering device, used in applications where the refrigerant flow rate is higher. These tubes are typically found in large-scale cooling systems, where they provide a simple and cost-effective means of regulating refrigerant flow. Float valves are used in applications where the refrigerant flow rate is variable, making them ideal for industrial refrigeration plants that require flexible and responsive temperature control.
Evaporator
The evaporator is a crucial component of an industrial refrigeration system, responsible for absorbing unwanted heat from the surrounding air or water and evaporating the refrigerant. In the industrial refrigeration cycle, the evaporator ensures that the refrigerant absorbs heat efficiently, maintaining the desired temperature and pressure within the system.
There are several types of evaporators used in industrial refrigeration systems. Air coil evaporators are the most common, typically used in applications where the ambient temperature is relatively low. These evaporators use air to transfer heat from the refrigerant, making them ideal for a wide range of industrial refrigeration applications.
Liquid coolers are used in environments where the ambient temperature is higher. These evaporators use liquid to absorb heat from the refrigerant, making them suitable for large-scale cooling systems. Plate heat exchangers are designed for very high ambient temperatures and are commonly used in industrial refrigeration plants. These heat exchangers provide efficient heat transfer, ensuring that the refrigerant evaporates effectively and the system operates at peak efficiency.
Refrigerants
Refrigerants are the lifeblood of an industrial refrigeration system, responsible for absorbing and transferring heat throughout the system. In the industrial refrigeration cycle, the refrigerant plays a crucial role in maintaining the temperature and pressure of the system, ensuring efficient and reliable operation.
There are several types of refrigerants used in industrial refrigeration systems, each suited to different applications. Ammonia is the most common refrigerant, known for its high efficiency and effectiveness in applications with high temperature and pressure requirements. Ammonia refrigeration systems are widely used in industries such as food processing and cold storage.
Carbon dioxide is another popular refrigerant, used in applications where the temperature and pressure requirements are relatively low. CO2 systems are gaining popularity due to their environmental benefits and are often found in large-scale cooling systems. Hydrofluorocarbons (HFCs) are used in applications with very high temperature and pressure requirements, making them suitable for industrial refrigeration plants.
Natural refrigerants, such as ammonia and carbon dioxide, are becoming increasingly popular due to their low environmental impact and high energy efficiency. These refrigerants are non-toxic and non-flammable, making them a safer choice for industrial refrigeration applications. As the industry moves towards more sustainable solutions, the use of natural refrigerants is expected to continue to grow, offering both environmental and operational benefits.
Types of Industrial Refrigeration Systems
Several types of systems are commonly used in industrial settings:
- Ammonia-based systems: Known for efficiency but require careful handling. GA Enns technicians are experts in safely managing ammonia systems.
- CO2 systems: Environmentally friendly and gaining popularity. Our "Climate-Friendly Cooling" solutions utilize CO2 to lower your carbon footprint.
- Freon-based systems: Less efficient but safer to handle.
- Cascade systems: Use multiple refrigerants for ultra-low temperatures.
Applications of Industrial Refrigeration
At GA Enns, we've implemented refrigeration solutions across various industries:
- Food Processing and Storage:
- Example: We installed a state-of-the-art ammonia refrigeration system for a large dairy processing plant in Mississauga, ensuring consistent temperatures for milk pasteurization and cheese aging.
- Cold Storage Warehouses:
- Example: Our team designed and maintains a multi-temperature cold storage facility in Kitchener, accommodating various products from frozen foods to fresh produce.
- Pharmaceutical Manufacturing:
- Example: GA Enns implemented a precision cooling system for a pharmaceutical lab in Toronto, maintaining exact temperatures for sensitive drug production.
- Ice Rinks:
- Example: We provide ongoing maintenance for several community ice rinks in Hamilton, ensuring perfect ice conditions year-round.
- Specialized Automation:
- Example: Our team integrated an automated cooling system for a craft brewery in Guelph, precisely controlling fermentation temperatures for consistent beer quality.
Benefits of Efficient Industrial Refrigeration
Implementing an efficient industrial refrigeration system offers several advantages:
- Increased efficiency and productivity
- Extended shelf life of perishable products
- Compliance with food safety regulations
- Significant energy savings over time
- Improved product quality and consistency
GA Enns: Your Partner in Industrial Refrigeration
At GA Enns, we offer comprehensive services to meet all your industrial refrigeration needs:
- 24/7 Emergency Service: Our team is always ready to respond to urgent issues. Call us at 647-643-4110 anytime.
- System Design: We create custom, innovative refrigeration solutions tailored to your specific needs.
- Installation and Maintenance: Our experts ensure your system runs at peak efficiency.
- Refrigerant Retrofit: We help you upgrade to eco-friendly, low GWP refrigerants.
- Compressor Rebuilds: Extend the life of your equipment with our expert rebuilding services.
- Refrigeration Operator Coverage: We help you comply with TSSA regulations effortlessly.
Future Trends in Industrial Refrigeration
The industrial refrigeration sector is evolving, and GA Enns is at the forefront:
- Natural Refrigerants: We're leaders in implementing CO2 and ammonia systems.
- IoT Integration: Our smart monitoring systems provide real-time data for improved efficiency.
- Energy Efficiency: We constantly innovate to reduce energy consumption and costs.
- Sustainability: Our solutions help you meet environmental goals and regulations.
How to Find the Best Industrial Refrigeration Contractors in Ontario
When seeking industrial refrigeration services in Ontario, consider these factors:
- Local Expertise: Look for companies like GA Enns with a strong presence in major Ontario cities.
- Industry-Specific Experience: Ask about experience in your particular industry.
- Emergency Response: Ensure 24/7 availability for critical issues.
- Comprehensive Services: Choose a provider offering design, installation, and maintenance.
- Sustainability Focus: Opt for contractors prioritizing energy efficiency and environmental responsibility.
Trust GA Enns for Your Industrial Refrigeration Needs
Industrial refrigeration is crucial for many businesses, impacting everything from food safety to manufacturing processes. As technology advances and environmental concerns grow, partnering with experienced local contractors becomes increasingly important.
GA Enns has been serving Ontario businesses for over 20 years, providing expert industrial refrigeration solutions in Toronto, London, Mississauga, Kitchener, Hamilton, Guelph, and beyond. Our team of skilled technicians, 24/7 emergency service, and commitment to innovation make us the ideal partner for all your industrial refrigeration needs.
Whether you're looking to install a new system, upgrade existing equipment, or ensure optimal performance through regular maintenance, GA Enns is here to help. Get in touch with our industrial refrigeration contractors.
Industrial Refrigeration Experts
Trusted by some of Ontario’s finest for over 20 years.
Speak With a Technician Today
.webp)