Compressor Overhauling: Step-by-Step Process & Tips
Learn the signs your compressor needs an overhaul, what's involved, and how regular maintenance boosts performance, extends lifespan, and prevents breakdowns.
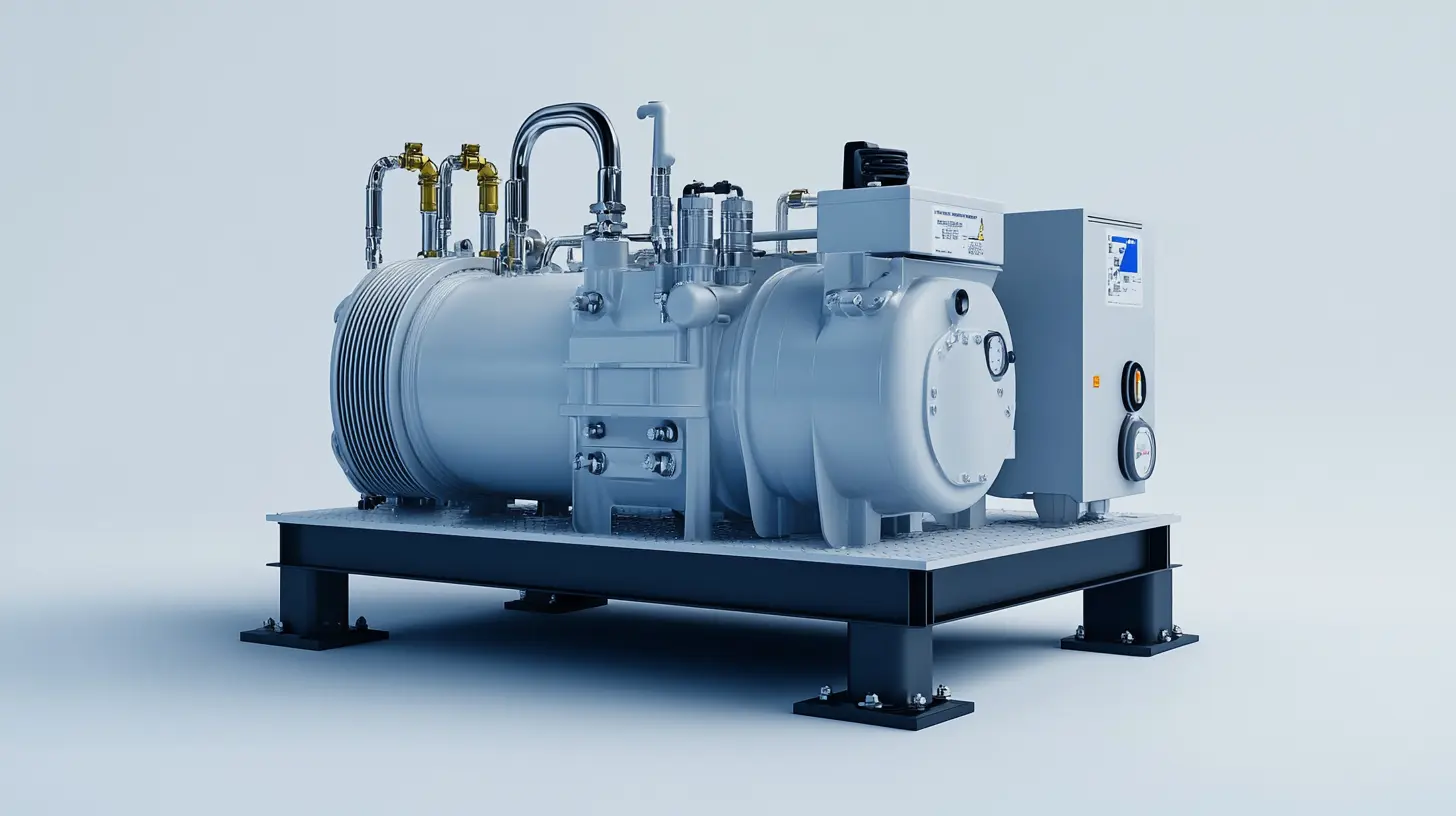
When a compressor begins to break down, the impact ripples through every function it serves, from industrial applications to everyday air conditioning units. Often humming quietly in the background, compressors are the unsung heroes of countless systems, driving the crucial flow of fluids that make many operations possible. However, like any mechanical component, compressors eventually wear out and require meticulous overhauls to restore optimal function and prevent costly breakdowns.
Understanding how compressor overhauls work is vital for anyone who relies on these machines. Overhauling is not merely a repair but a comprehensive rejuvenation process that addresses wear and tear, replaces essential components, and ultimately revitalizes performance. This proactive approach can dramatically extend the machine’s lifespan, enhance its efficiency, and avoid major failures that disrupt operations and inflate repair costs.
In this article, we will explain the process of compressor overhauling, from identifying the telltale signs of a struggling compressor to the steps involved in bringing it back to life. We’ll explore the benefits of regular maintenance, the costs involved, and offer guidance on choosing a reliable service provider like Enns Industrial Refrigeration to ensure your compressor continues to operate at peak efficiency.
What is compressor overhauling?
Compressor overhauling is the process of inspecting, repairing, and maintaining compressors to ensure optimal performance and extend their service life. Compressors, like rotary screw and centrifugal types, are vital in industrial operations. Overhauling prevents issues such as oil contamination or compressor malfunction.
A minor service is different from a complete overhaul. Minor service involves routine tasks like cleaning suction filters and checking the pressure switch. It ensures daily operation runs smoothly.
In contrast, a complete overhaul is more thorough. It involves disassembling the compressor, replacing worn-out parts, and testing functional aspects. This includes:
- Testing of oil flow
- Checking discharge pressure
- Inspecting for oil contamination
- Cleaning of rotary screws
- Functional testing for peak performance
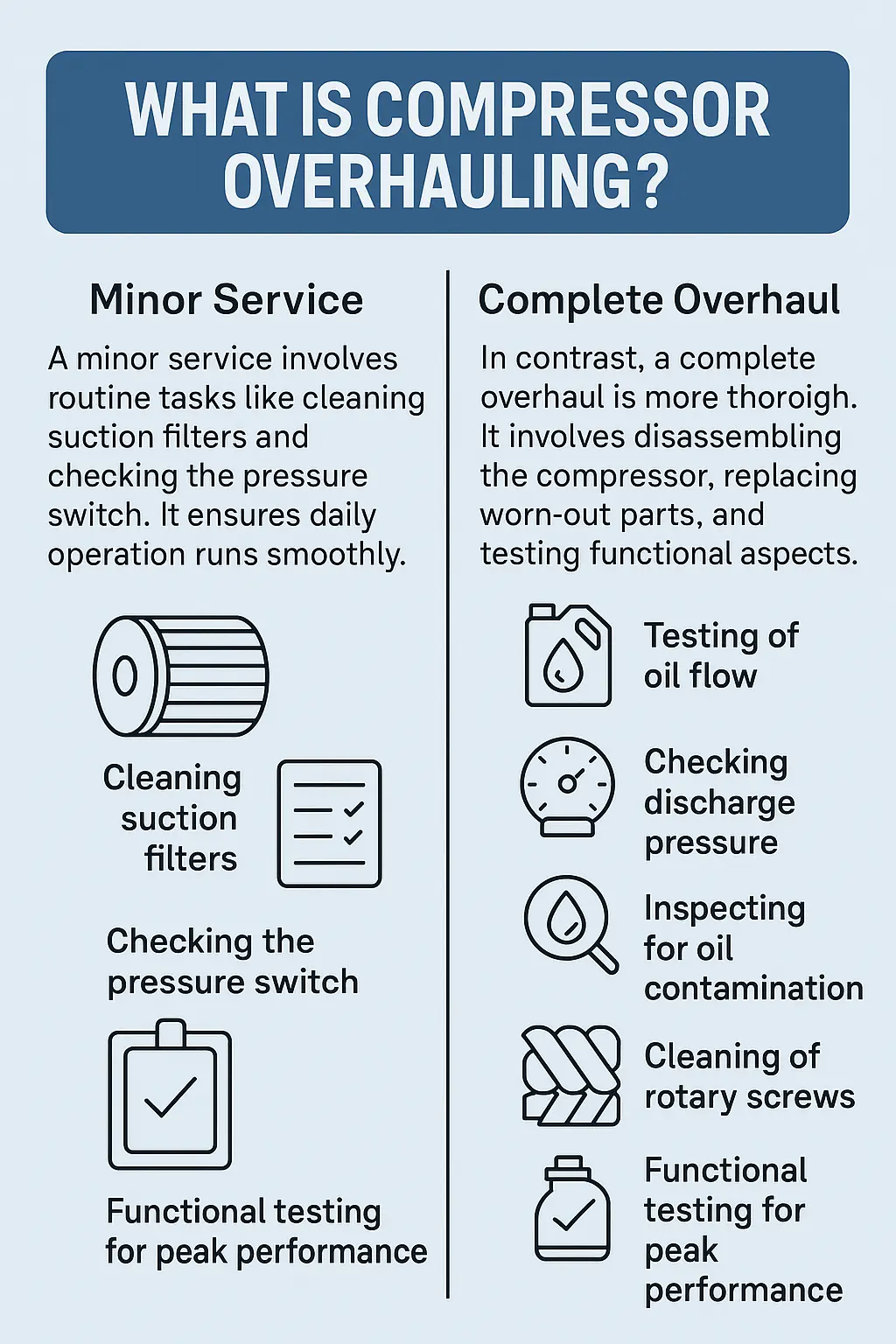
Below is a simple comparison:
Signs your compressor needs an overhaul
Is your compressor showing signs of wear and tear? Here are key indicators that it might need an overhaul for optimal performance:
- Reduced Performance and Efficiency
If your compressor isn’t operating at peak performance, it may struggle to meet demand, causing inefficiency. - Unusual Noises or Vibrations
Strange sounds or vibrations could signal issues with rotary screws or internal components. - Increased Operating Temperatures
High internal compressor temperatures can lead to oil contamination. - Frequent Breakdowns or Shutdowns
Regular failures can increase energy consumption and cause the compressor to malfunction. - Oil Leaks or Contamination
Watch for oil contamination with metal fragments, or leaks, which affect the compressor's service life.
How to tell if your compressor needs immediate attention:
- Unusual Noises: Rotary Screw Compressor Issues
- High Temperatures: Pressure and Temperature Concerns
- Oil Leaks: Check Oil Filter and Suction Filters
Addressing these issues with a screw compressor overhaul or contacting refrigeration and compressor maintenance experts like Enns Industrial will ensure longer service life and fewer operational halts. Always refer to the service manual and consider functional testing for a well-maintained compressor.
Benefits of a compressor overhaul
Overhauling a compressor is vital for maintaining its performance and longevity. Regular use and normal wear and tear can lead to inefficiencies, increased energy consumption, and potential breakdowns. A timely overhaul ensures that your industrial air compressor operates smoothly, minimizing downtime and costs. This proactive approach not only addresses existing issues but also prevents future malfunctions. By focusing on comprehensive maintenance, you ensure your compressor remains at peak performance. Furthermore, consistent upkeep can reduce the likelihood of contamination and improve the reliability of your equipment. Let's explore the specific advantages of conducting a compressor overhaul.
1. Extend compressor lifespan
A compressor overhaul is crucial for extending its service life. Regular maintenance checks prevent small issues from becoming significant problems. Addressing wear and tear promptly avoids costly replacements or repairs. By replacing damaged compressor parts, like filters or rotary screws, you can enhance the compressor's longevity. Proper cleaning of suction filters and ensuring the oil filters are uncontaminated will keep the system running smoothly. When components are inspected and repaired as needed, the risk of catastrophic failures decreases. Regular overhauls, guided by the service manual, keep the compressor functioning well beyond its expected service life.
2. Improve compressor performance
Increasing performance is a primary benefit of regular compressor overhauls. By addressing inefficiencies, you ensure the compressor meets operational demands. Performing functional testing, such as testing for oil leaks and checking position transmitters, identifies performance issues early. Removing contamination and ensuring clean oil flow helps maintain peak performance. Additionally, addressing potential blockages in the rotary screws or other components can significantly improve efficiency. Overhauls also adjust the pressure switch and discharge pressure settings, optimizing energy consumption. With improved performance, the compressor supports industrial processes without unnecessary energy costs or shutdowns.
3. Prevent major compressor failures
Preventing major failures through regular overhauls is vital to avoid unforeseen disruption. By monitoring internal compressor temperatures and addressing abnormalities, you can help prevent unexpected breakdowns. Overhauls help you identify and fix issues before they escalate. For example, an unchecked oil contamination issue could lead to significant damage if ignored. Regularly overhauled compressors are less likely to experience catastrophic failures, reducing operational risks. Through methodical inspections and maintenance, compressors are less prone to malfunction. Consistent attention to potential warning signs ensures that major failures are prevented, securing continuous and reliable operation.
When to schedule a compressor overhaul
Compressor overhauls are crucial for sustaining optimal performance. Scheduling them at the right time enhances the service life and prevents malfunctions.
Recommended Operating Hours: Different compressors suggest varying operating hours before an overhaul. Typically, guidelines are provided by manufacturers.
Manufacturer Guidelines: Always refer to the service manual. These guidelines include specific recommendations which are vital for maintaining peak performance.
Factors Influencing Overhaul Frequency:
- Environment: Dusty areas lead to quicker contamination. This necessitates frequent Cleaning of suction filters.
- Load Conditions: Workloads differ. Heavy-duty operations require more frequent overhauls.
- Temperature Variations: Fluctuations alter internal compressor temperatures, affecting the service life.
Regular functional testing and product testing, such as testing for oil leaks and the position transmitters, are advised. If you notice any irregularities like oil contamination with metal fragments or a pressure switch issue, immediate maintenance is necessary. For reliable preventative and maintenance compressor services, consider professionals like Enns Industrial Refrigeration Services.
Steps involved in compressor overhauling
Overhauling compressors is crucial for maintaining optimal performance and extending service life. The process involves several steps to ensure the compressor functions effectively. Here's a concise overview of the overhaul process:
- Inspection and Disassembly: First, inspect the compressor to identify any issues. Carefully disassemble the unit for detailed examination.
- Cleaning and Assessment: Clean all components, including suction filters, to remove contaminants. Assess each part for wear or damage, focusing on areas prone to contamination with metal fragments or oil contamination.
- Replacement of Components: Replace worn or damaged components, such as rotary screws or oil filters, to prevent malfunction and high energy consumption.
- Reassembly and Recalibration: Reassemble the compressor, ensuring precise alignment. Recalibrate settings like discharge pressure and pressure switch for peak performance.
- Testing and Performance Verification: Conduct comprehensive testing. This includes functional testing, testing for oil leaks, and verification of internal compressor temperatures and oil flow.
Here is a table summarizing the steps:
Following these steps will ensure the compressor operates effectively and efficiently.
Common parts replaced during a compressor overhaul
When overhauling compressors, certain parts commonly require replacement to ensure optimal performance and extend service life, such as:
- Bearings - Essential for smooth operation; worn bearings can lead to increased energy consumption.
- Seals and Gaskets - Prevent leaks; compromised seals can cause oil contamination or compressor malfunction.
- Valves - Critical for controlling pressure; faulty valves can affect discharge pressure and daily operation.
- Pistons or Rotors - Key in rotary screw and centrifugal compressors; damage can cause internal compressor temperatures to rise.
- Oil Filters and Lubrication Systems - Vital for removing contaminants like metal fragments and ensuring proper lubrication.
Step-by-Step compressor overhaul process
Overhauling compressors is a task that demands meticulous attention to detail and adherence to specific protocols. To achieve optimal performance and extend the lifespan of compressors, a systematic approach is essential. This process includes several critical stages, from initial inspection to final testing. By following these steps, technicians can ensure that the compressor operates efficiently and without unexpected interruptions. The overhaul process not only prevents potential issues but also enhances the overall reliability and energy efficiency of the equipment.
1. Initial inspection and assessment
Before beginning a compressor overhaul, conduct a thorough inspection and assessment. This step is crucial to identify any existing issues that might affect the compressor's performance. Inspecting the compressor involves examining all components, from seals and gaskets to pistons or rotors, for signs of wear or damage. Assess the discharge pressure and internal temperatures to understand the current state of the equipment. This initial evaluation helps in planning the overhaul and deciding which parts need replacement or repair. It's the foundation that ensures the rest of the overhaul process runs smoothly.
2. Verifying motor rotation
Ensuring correct motor rotation is a critical step after reassembling the compressor. Incorrect rotation can cause the compressor to malfunction and lead to additional issues. Start by confirming the motor's direction of rotation aligns with the manufacturer's specifications. Use functional testing to ensure that the motor operates smoothly without any abnormal noises or vibrations. Verifying the motor rotation contributes to the overall stability and functionality of the compressor, ensuring it can handle daily operations without unexpected breakdowns or inefficiencies.
3. Flushing oil circuits
Flushing the oil circuits is a vital step to prevent oil contamination and ensure a clean lubrication system. This process removes any contaminants, such as metal fragments, that could harm the compressor. Begin the flushing by using a suitable cleaning solution, circulated through the oil system, to dislodge and remove impurities. Continuously monitor and test the oil flow to ensure all contaminants are cleared. Properly flushed oil circuits help maintain the internal compressor temperatures and contribute to the compressor's peak performance. This process ensures the longevity and efficiency of the compressor.
4. Reassembly and final testing
After cleaning and replacing all necessary components, reassemble the compressor with precision. Carefully follow the service manual to avoid any errors. Once reassembled, perform a set of product tests to validate the overhaul. These tests should include checking for oil leaks, ensuring proper oil flow, and testing the position transmitters for accuracy. Final testing is critical as it confirms the compressor's readiness for regular operations. Ensuring everything functions as intended will boost confidence in the equipment's reliability and performance, protecting the investment in the overhaul process.
Choosing the right service provider for compressor overhauls
Selecting the right partner for compressor overhauling is crucial. Look for providers who offer:
- Certifications and expertise: Technicians should be factory-trained and certified.
- Experience and references: Proven track record with similar compressors and industries.
- OEM parts and quality assurance: Using original industriaparts maintains equipment integrity.
- Service guarantees and support: Reliable companies stand behind their work.
GA Enns is a trusted refrigeration compressor rebuilder in Ontario, with decades of experience handling compressor overhauls for businesses in Toronto, Kitchener, Waterloo, Cambridge, Guelph, Elora, Hamilton, Mississauga, Niagara Falls, Ottawa and Oakville.
Our team offers thorough inspections, genuine replacement compressor parts, and detailed performance testing, ensuring equipment returns to peak performance standards.
Working with local experts like GA Enns also offers logistical advantages, including faster turnaround times and familiarity with the regional industrial requirements.
Learn more about our industrial cooling services in Ontario.
Costs associated with compressor overhauling
Overhauling a compressor can be a cost-effective way to extend its service life. The cost varies based on several factors. These include the size of the compressor, its brand, current condition, and the parts needed for the overhaul.
The typical price range for an overhaul starts at a few hundred dollars and can go up to several thousand dollars.
Compared to replacement, overhauling is generally cheaper. Purchasing a new industrial air compressor can cost significantly more. Overhauling can optimize performance without the high upfront cost.
Here's a quick comparison:
- Overhaul: Lower cost, extends existing compressor's life
- Replacement: Higher cost, brand new unit
In conclusion, choosing an overhaul over replacement can save money and energy by keeping the compressor functional. Proper maintenance ensures optimal performance and prolongs peak efficiency.
Preventive maintenance tips after an overhaul
Preventive maintenance ensures your compressor runs smoothly after an overhaul. Follow these simple tips to maintain a functional compressor.
- Regular Inspections: Schedule regular inspections to check for wear and tear. Look for signs of contamination with metal fragments and oil contamination.
- Monitor Operating Parameters: It's essential to watch key parameters like discharge pressure and internal compressor temperatures. Use pressure switches to alert you to any issues.
- Detailed Maintenance Records: Keep records of all maintenance activities. This helps track when the rotary screws or oil filters need replacing.
- Staff Training: Train your staff to recognize signs of peak performance and potential issues. Awareness can prevent a compressor from malfunctioning.
Here's a quick checklist for daily operation:
Frequently Asked Questions (FAQs) about Compressor Overhauls
What is the typical lifespan of a compressor after an overhaul?
A properly overhauled compressor can operate efficiently for several more years, often adding 5,000 to 10,000 operating hours, depending on conditions and maintenance.
How long does a compressor overhaul take?
Most overhauls are completed within a few days to two weeks, depending on compressor type, availability of parts, and extent of service required.
Can I perform a compressor overhaul in-house?
While minor maintenance can be performed internally, full overhauls should be handled by qualified industrial compressor service professionals such as those at GA Enns, ensuring proper techniques and OEM parts are used.
Is it better to overhaul or replace a compressor?
If the compressor casing and critical components are in good condition, overhauling is often far more economical than full replacement.
What types of compressors require overhauls?
All major compressor types, including reciprocating, rotary screw, centrifugal, and scroll compressors, require overhauls at specified intervals to maintain reliability and performance.
Industrial Refrigeration Experts
Trusted by some of Ontario’s finest for over 20 years.
Speak With a Technician Today
.webp)