Understanding CO2 Refrigeration: Key Concepts and Applications
Find out how CO₂ refrigeration offers low environmental impact and up to 30% higher energy efficiency. Learn key concepts and applications for sustainable cooling.
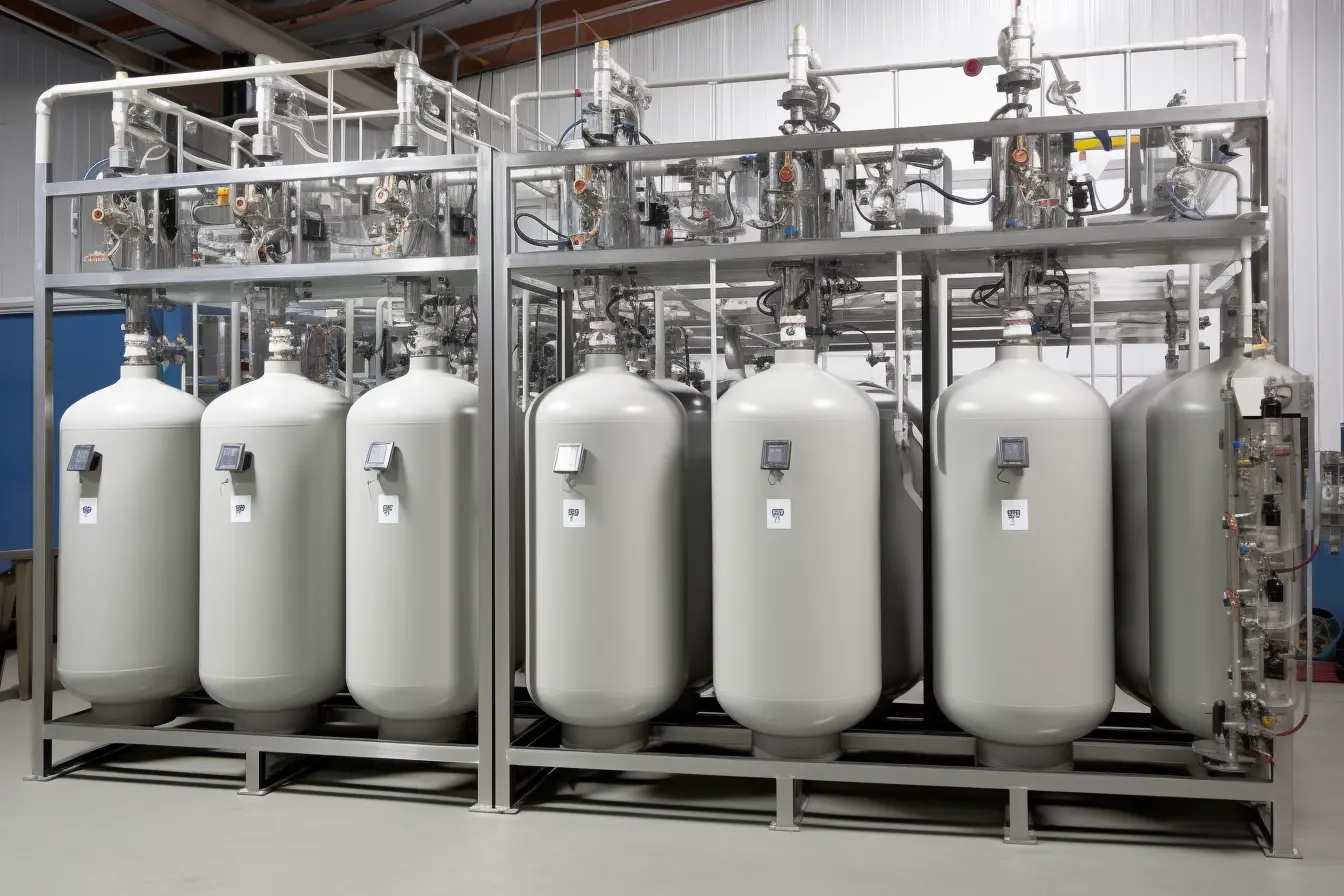
Rising global temperatures and increasing environmental concerns have heightened the need for sustainable refrigeration solutions. CO₂ refrigeration has emerged as a frontrunner among natural refrigerants, celebrated for its exceptionally low environmental impact and high efficiency. Remarkably, CO₂ (R-744) boasts a global warming potential (GWP) of just 1, starkly contrasting with traditional refrigerants like R-404a, which have GWPs exceeding 3,900. This significant difference makes CO₂ refrigeration a crucial player in the effort to reduce the carbon footprint of cooling systems worldwide.
The advantages of CO₂ refrigeration extend well beyond its environmental benefits. Modern CO₂ systems can achieve up to 30% higher energy efficiency compared to conventional refrigeration methods, leading to substantial cost savings and reduced energy consumption for businesses. Central to this efficiency are the system’s key components—the compressor, gas cooler, expansion valve, and evaporator—which collaborate seamlessly to deliver superior cooling performance. Innovations in compressor technology, especially the integration of scroll compressors, have further enhanced the reliability and effectiveness of CO₂ refrigeration systems, making them suitable for a diverse range of applications from supermarket chains to industrial cold storage facilities.
This article explores the fundamental principles of CO₂ refrigeration, highlighting its superiority over traditional refrigerants like ammonia. It delves into the essential design considerations for optimizing transcritical systems and examines the regulatory frameworks that are accelerating the adoption of CO₂ technology. By uncovering these key concepts and applications, we aim to shed light on the pivotal role CO₂ refrigeration plays in advancing sustainable development and shaping the future of efficient cooling solutions.
The Importance of CO2 as a Natural Refrigerant
CO2 is gaining traction as a natural refrigerant, thanks to its eco-friendly attributes. It has zero Ozone Depletion Potential (ODP) and a Global Warming Potential (GWP) of just 1. This makes it a smart choice for reducing the carbon footprint of refrigeration systems.
Advantages of CO2 Refrigeration:
- High Efficiency: CO2 systems operate efficiently even at high condensing temperatures, leading to energy savings and lower operating costs.
- Excellent Thermo-physical Properties: Natural CO2 has high thermal conductivity and refrigerating capacity per unit volume. This results in improved cooling efficiency.
- Safe and Stable: CO2's physical stability enhances its safety in various applications.
- Lower Compression Pressure Ratio: Compared to synthetic refrigerants like HFCs, CO2 offers better volumetric efficiency.
CO2 refrigeration systems are particularly beneficial in commercial and industrial applications. They deliver significant energy savings, which translates to lower cost of ownership over a period of time. Food retailers and other businesses using CO2 systems can expect reduced energy consumption and decreased environmental impact. With increasing reliance on natural refrigerants, CO2 is a promising alternative to traditional refrigeration systems.
Fundamental Components of CO2 Refrigeration Systems
CO2 refrigeration systems are built from several fundamental components. Each part plays a crucial role in ensuring the system's efficiency and effectiveness. Here's a breakdown of these components:
Compressor
The compressor is the powerhouse of a CO2 refrigeration system. It compresses the refrigerant, initiating the cooling cycle. CO2 compressors operate at high pressures and feature small structural sizes. They have higher pressure differences between suction and exhaust compared to other refrigerant compressors. Common types include Piston, Rolling Piston, Swing Piston, Scroll, Vane, and Screw compressors. These are designed for the unique properties of CO2, ensuring high cooling and heating efficiencies. Leading manufacturers like Danfoss, Bitzer, Dorin, and Emerson are at the forefront of developing these compressors to meet market demand.
Gas Cooler
The gas cooler, often called a condenser, is responsible for releasing heat from the refrigerant. This process transforms the gas into a high-pressure liquid. An adiabatic gas cooler uses wetted pre-cooling pads. This delays CO2 systems from entering transcritical mode, boosting energy efficiency during high ambient temperatures. These coolers can handle pressures up to 1,740 PSIG (120 bar) and are useful in applications like process cooling, blast freezing, and HVAC/R. Features such as axial EC fan technology and epoxy-coated fins enhance their durability and efficiency.
Expansion Valve
The expansion valve manages the flow of high-pressure CO2. It causes a pressure drop, creating a mixture of liquid and vapor. In booster systems, there are four types of expansion valves: high-pressure, flashgas bypass, MT, and LT expansion valves. Each controls pressure at different stages of the cycle. The high-pressure valve reduces refrigerant pressure from about 90 bar to 38 bar before moving it to a flash tank. MT valves adjust pressure for medium-temperature evaporators, while LT valves are for low-temperature ones.
Evaporator
The evaporator's role is to absorb heat from the refrigerated space, creating a cooling effect. In CO2 systems, it converts CO2 from liquid to vapor while absorbing latent heat. Effective evaporator operation is vital for system efficiency. In transcritical booster systems, it boils and expands CO2 into superheated vapor before compression. The evaporator runs at pressures much lower than compressor discharge, typically around 200 PSIG in low-temperature applications. This component's effective heat absorption is crucial to the refrigeration system's overall performance.
How CO2 Refrigeration Systems Function
CO2 refrigeration systems are an eco-friendly choice for cooling solutions. These systems operate above CO2's critical temperature of 87.8°F. They use a gas cooler to remove heat efficiently. The process involves high-pressure expansion valves which control refrigerant flow into the evaporator.
Here’s a simplified breakdown of how it functions:
- Supercritical Phase: CO2 is first boiled into a superheated vapor.
- Throttling: This even distribution through pipes reduces system size.
- Subcritical Phase: The CO2 returns to a liquid form, completing the cycle.
The standout feature of CO2 systems is their environmental advantage. With an Ozone Depletion Potential (ODP) of 0 and a Global Warming Potential (GWP) of 1, CO2 is a sustainable alternative to traditional refrigerants like CFCs and HCFCs. These systems are compact, saving space and energy.
Advancements in system control technology have made CO2 transcritical booster systems easier to operate, increasing their popularity in commercial and industrial applications. This efficiency is especially useful in the cold chain and food retail sectors where reducing energy consumption and carbon footprint is crucial.
Innovations in CO2 Compressor Technology
CO2 compressor technology is advancing rapidly. Thanks to CO2's high evaporation latent heat and refrigerating capacity per unit volume, compressors are becoming more efficient. This efficiency allows for smaller and more compact refrigeration systems. The excellent flow and heat transfer capabilities of CO2, due to its low kinematic viscosity and high thermal conductivity, further shrink compressor equipment size.
These characteristics make CO2 a top choice in modern refrigeration solutions. It is environmentally friendly with an Ozone Depletion Potential (ODP) of 0 and a Global Warming Potential (GWP) of 1. This makes it a sustainable option for compressor technology. Additionally, CO2's stable chemical properties ensure reliable operation in refrigeration cycles. This stability helps maximize compressor performance across different applications.
Continuous technological advancements are making transcritical CO2 systems highly competitive. They are beginning to rival traditional synthetic refrigerant systems. This is leading to innovations in compressor design and increasing their efficiency.
Focus on Scroll Compressors
CO2 scroll compressors stand out in the world of refrigeration. Known for low vibration and low noise, they also boast longevity and reliability. Their high efficiency makes them a preferred choice in many systems. These compressors promise promising development prospects, especially compared to other types in the small and medium cooling capacity market.
Why are CO2 scroll compressors so important? They enhance the overall efficiency of refrigeration systems. For refrigeration to work well, the proper functioning of a compressor is vital. It ensures effective refrigerant circulation throughout the system.
The market for small and medium cooling capacity compressors is shifting. CO2 scroll compressors, with their beneficial features, are set to capture a significant share. This positions them as a key player in the push for greener and more efficient cooling solutions.
Comparison of CO2 with Other Refrigerants
CO2, or Carbon Dioxide, is a natural refrigerant known for its low Global Warming Potential (GWP) of one. This makes it an ideal benchmark when comparing the environmental impact of other refrigerants. Unlike synthetic refrigerants, CO2 systems are more efficient. They use smaller compressors and pipes, resulting in compact refrigeration systems.
CO2 is non-toxic and non-flammable, aligning well with current regulations. This means it presents fewer risks for future regulatory changes compared to other refrigerants. Although CO2 systems are 15-25% more expensive than synthetic ones initially, they prove to be cost-effective in the long run. Their installation costs are about 10-12% less, which makes them a smart financial choice over time. Additionally, CO2 systems have high Coefficient of Performance (COP) values. They achieve great cooling with less energy, reducing electricity bills compared to traditional refrigerants.
Advantages of CO2 vs. Ammonia
CO2 refrigeration systems are non-toxic and chemically stable. They do not contain PFAS, making them safer than ammonia-based systems, which are caustic and can cause corrosion. CO2's GWP is much lower at one, meaning it faces less regulatory pressure compared to ammonia. CO2 systems also have fewer outages. Ammonia can corrode seals and gaskets, reducing system reliability.
Installation costs for CO2 systems are about 10-12% lower than ammonia systems with similar designs. This offers both economic and operational benefits. Moreover, CO2 systems allow for effective heat recovery with little extra investment. This makes them more versatile than ammonia systems, which might struggle with heat recovery.
Challenges and Limitations
CO2 refrigeration systems must work at high operating pressures. The trans-critical cycle requires up to 10 MPa, necessitating strict design standards. CO2's low critical temperature of 31.1 ℃ can be a challenge, especially in warmer climates. High ambient temperatures can limit its effectiveness in refrigeration cycles.
Shifting to CO2 systems means the industry must adapt to using natural refrigerants instead of traditional synthetic ones. In warmer climates, transcritical CO2 systems may consume more energy, which raises efficiency concerns. Although high-pressure components have improved CO2 system efficiency, challenges with energy use in specific conditions persist.
Operational Benefits of CO2 Refrigeration
CO2 refrigeration systems offer many benefits over traditional systems. One major advantage is their reduced energy bills. This is due to their high Coefficient of Performance (COP) values. These systems provide optimal cooling with minimal energy use. Moreover, CO2 systems use smaller piping and low pumping power, leading to higher efficiency and space savings.
CO2's high thermal conductivity and favorable density help create compact systems. This enhances flow and heat transfer performance. Additionally, CO2 is a safe choice because it is non-toxic and noncombustible. It remains stable even at high temperatures, avoiding harmful gas emissions. CO2 refrigeration can also recover heat effectively, boosting system efficiency further.
Energy Efficiency
CO2 refrigeration solutions can be up to four times more energy efficient than traditional systems. This significantly simplifies cold chain management and leads to lower energy bills. Venues that have adopted CO2 systems report noticeable savings. Advanced technologies, such as transcritical CO2 systems, enhance energy efficiency. These include high-efficiency gas coolers and axial EC fans.
The good thermal conductivity of CO2 improves flow and heat transfer performance. This means that compressors and equipment can be smaller and more efficient. CO2 systems are designed for a lower total cost of ownership and longer use. They operate with custom capacities to match needs, reducing excess capacity and optimizing energy use.
Environmental Sustainability
CO2 has a Global Warming Potential (GWP) of 1, making it a sustainable and natural option. It is far better than traditional synthetic refrigerants in this regard. CO2 also has an Ozone Depletion Potential (ODP) of 0, meaning it does not harm the ozone layer. This fact further enhances its environmental sustainability.
By using CO2, businesses can recycle industrial by-products, delaying greenhouse gas emissions. Switching to CO2 refrigeration aligns with international environmental regulations. This future-proofs business investments and underscores a commitment to sustainable practices. Adopting CO2 technology also plays a significant role in preserving the planet by reducing impact on global warming.
Design Considerations for Transcritical Systems
When designing CO2 transcritical systems, several key factors come into play to ensure efficiency and reliability. A stable baseline of performance starts with proper configurations of the gas cooler, high-pressure valve, and flash tank. This involves controlling variable fan speeds and modulating high-pressure and bypass gas valves.
Key Design Elements:
Pressure Management:
Incorporate pressure-relief valves in each zone for safe refrigerant release during extended shutdowns.
Use auxiliary condensing units with backup generators to maintain pressure during power outages.
Efficiency Enhancements:
Leverage technological advancements to achieve lower minimum condensing temperatures, especially effective at lower ambient temperatures.
Integrate evaporative cooling to boost efficiency in warmer climates.
System Components: